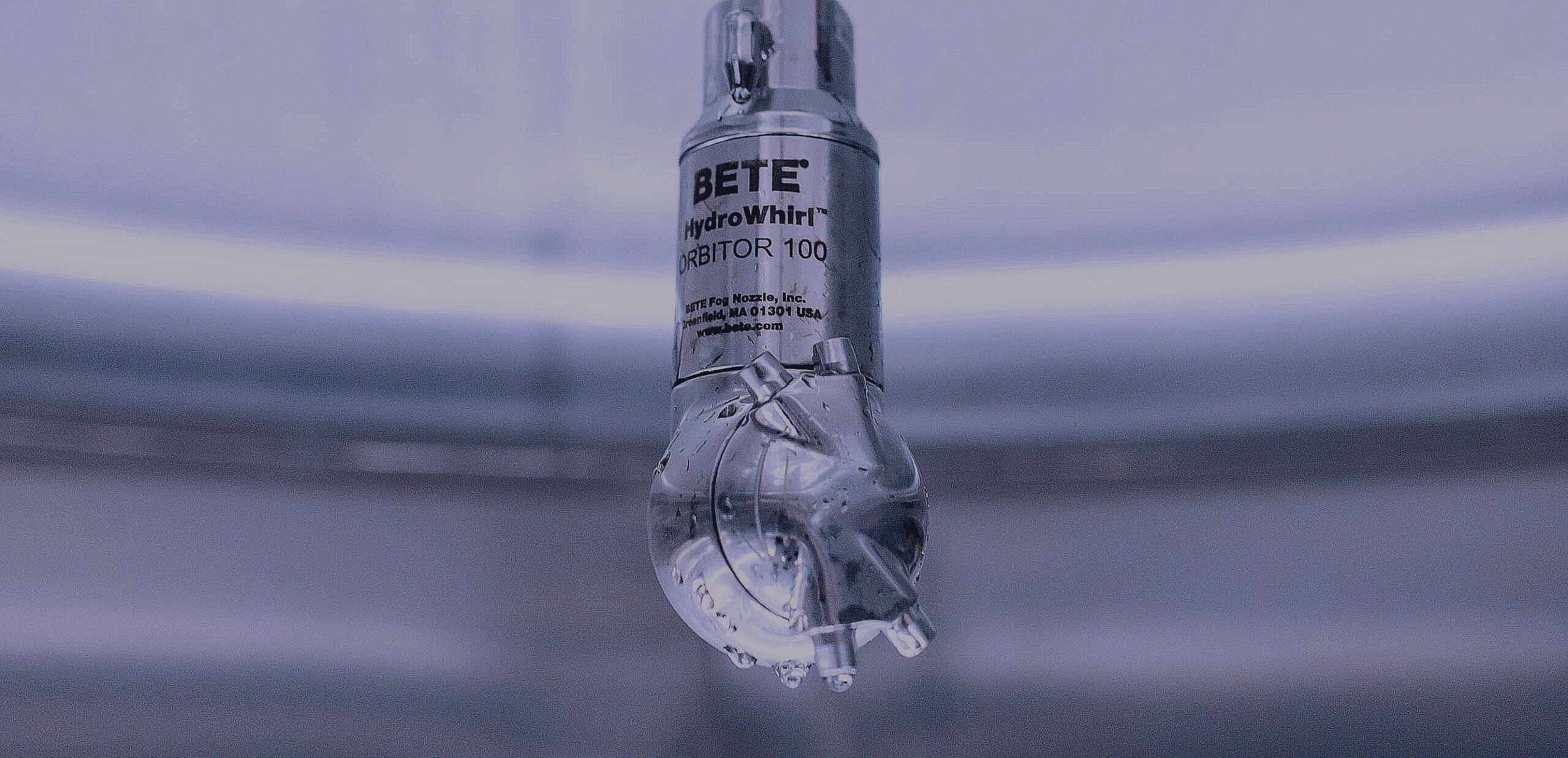
HiDur® Inert Balls - Random packings
HiDur® Inert Balls are the simplest, regular formed type of random packing, with relatively small surface area per packed volume. Due to the low void fraction, pressure drop is quite high.
HiDur® Inert Balls are mainly used as catalyst carriers and flow straighteners at refineries and other petrochemical industries.
- Product information
- Technical data
- Documentation & videos
- Checklist process data
- General info Column internals
- Supplier information
- Send saved products to yourself, or as a quote request to Hansa
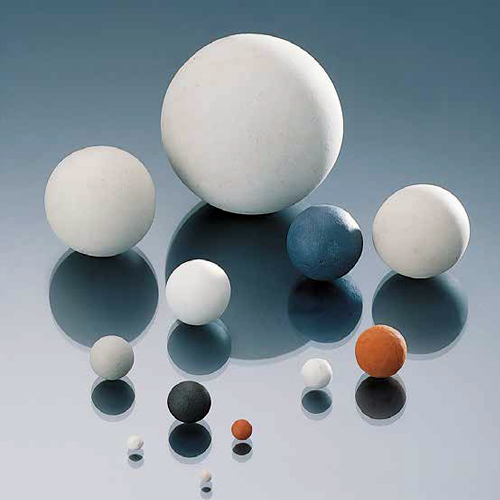
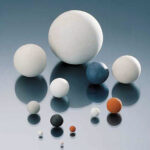
Design features
- Simplest design of all types of random packings
- Relatively small surface area per bed volume, low void fraction and high pressure drop
- Mainly used as a catalyst carrier and flow straighteners at refineries and other petrochemical industries
Listed below are different sizes of HiDur® Inert Balls. Under the tab 'Documentation & videos' you will find data sheets with additional information.
HiDur® Inert Balls
Data refer to stoneware | ||||||||||||
---|---|---|---|---|---|---|---|---|---|---|---|---|
Type size | Weight kg/m3 | Surface area m2/m3 | Void fraction in % | |||||||||
1/8" | 1350 | 720 | 44 | |||||||||
1/4" | 1350 | 520 | 44 | |||||||||
3/8" | 1350 | 360 | 44 | |||||||||
1/2" | 1350 | 275 | 45 | |||||||||
5/8" | 1350 | 220 | 45 | |||||||||
3/4" | 1350 | 190 | 45 | |||||||||
1" | 1350 | 144 | 45 | |||||||||
1 1/4" | 1350 | 120 | 45 | |||||||||
1 1/2" | 1350 | 100 | 45 | |||||||||
2" | 1350 | 72 | 45 |
Available materials: Stoneware, and aluminium oxide
Download PDF
Checklist important parameters
Listed below are a number of parameters that are important to consider when selecting the right type and size of random packing in order to achieve an effective and sustainable solution.
Sometimes it is difficult or even impossible to obtain information and data regarding the specific process. Together with our suppliers, we have extensive experience and we can make sound assumptions as a basis for designing the best solution for the process.
Operating data | |||||||||||
---|---|---|---|---|---|---|---|---|---|---|---|
Gas | Unit | ||||||||||
Type of gas | Please state | ||||||||||
Gas volume flow (operating conditions) | m3/h | ||||||||||
Gas density (operating conditions) | kg/m3 | ||||||||||
Gas viscosity | mm2/s (cP) | ||||||||||
Operating pressure | bar (a) | ||||||||||
Operating temperature | °C |
Operating data | |||||||||||
---|---|---|---|---|---|---|---|---|---|---|---|
Liquid | Unit | ||||||||||
Type of liquid | Please state | ||||||||||
Liquid volume flow | m3/h | ||||||||||
Liquid density | kg/m3 | ||||||||||
Liquid viscosity | cP | ||||||||||
Surface tension | mN/m |
Geometrical data | |||||||||||
---|---|---|---|---|---|---|---|---|---|---|---|
Data | Info/unit | ||||||||||
Packing type and size | Please state (if known) | ||||||||||
Specific surface area | m2/m3 (if known) | ||||||||||
Packing height | mm | ||||||||||
Column diameter | mm |
Additional information/requirements | |||||||||||
---|---|---|---|---|---|---|---|---|---|---|---|
Data | Info/unit | ||||||||||
Material | Please specify | ||||||||||
Fouling | Yes/No | ||||||||||
Foaming | Yes/No | ||||||||||
Other requirements/additional information | Please specify |
Optimised performance in mass and heat transfer processes
For optimised performance in a mass or heat transfer process it is important to understand the underlying principles and parameters that are important to consider when designing a column for flue gas cleaning, flue gas condensation or stripping.
Founded in 1976, RVT Process Equipment is a leading supplier and manufacturer of droplet separators, packings, column internals and other products for mass and heat transfer processes.
RVT Process Equipment offers advanced engineering and technical support and has extensive experience in various processes and applications in the chemical and petrochemical industry, refineries, power plants, and pulp and paper. The R&D department houses fully equipped test units, available to carry out customer-specific tests when needed.
RVT Process Equipment has subsidiaries and manufacturing facilities in Knoxville, USA and in Kunchan, China.
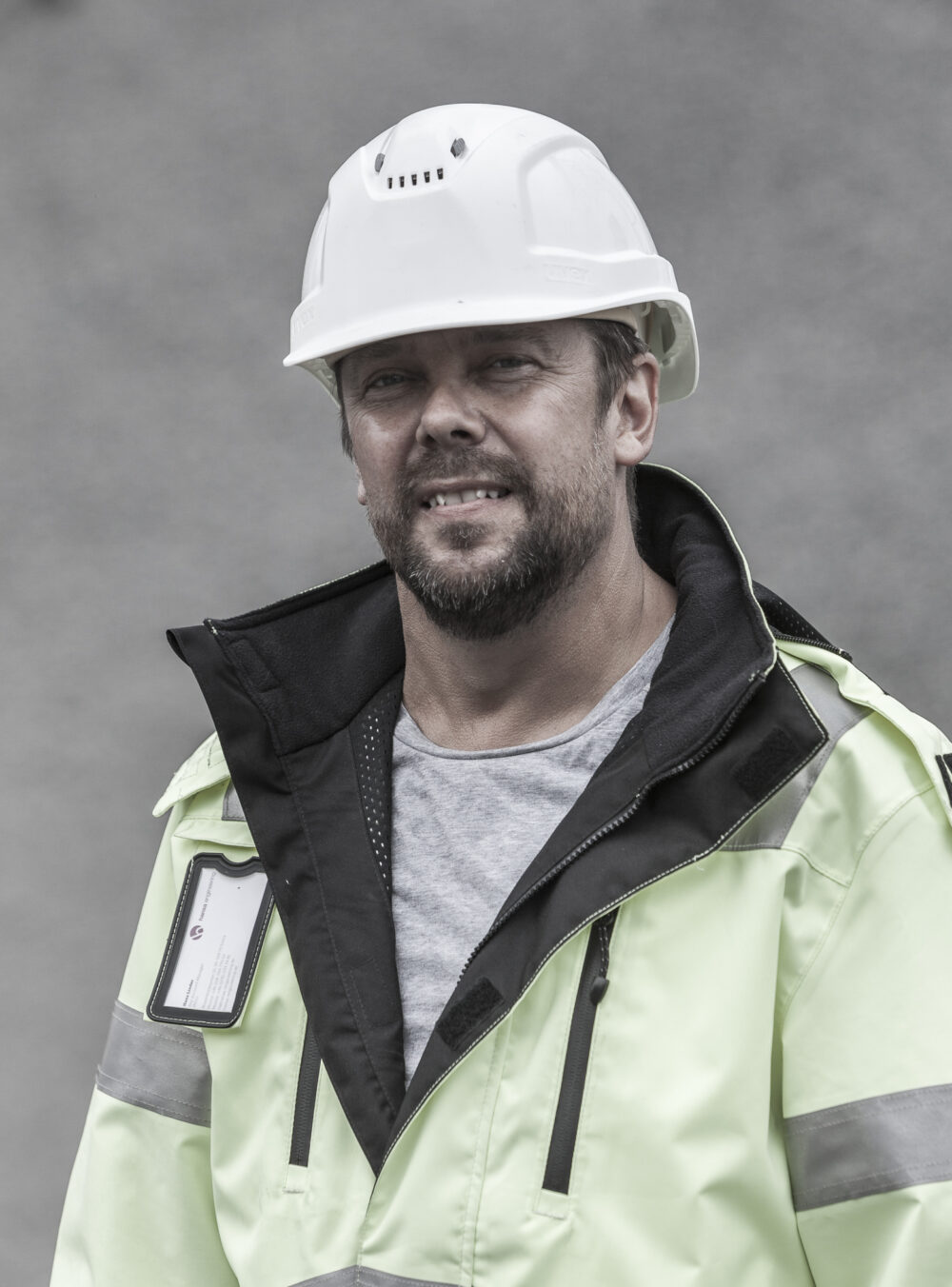
Our customer promise
Right solution, technical expertise and commitment is what you can expect from us as your partner or supplier.
Support & service
We offer the support you need to optimise your process and develop a sustainable solution.
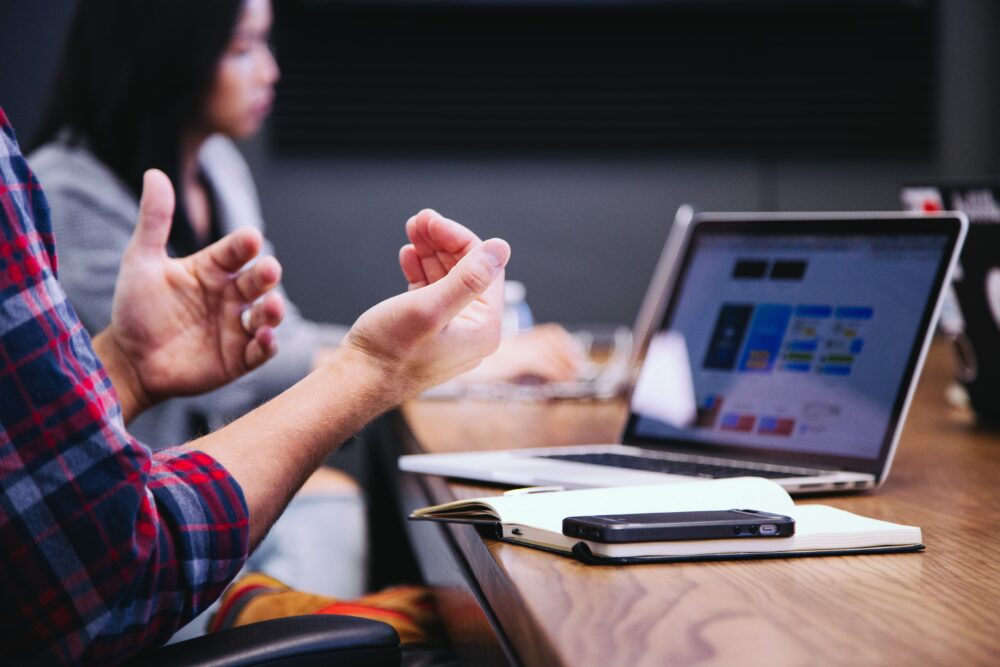
Right solution, delivered on time
Delivering the right solution on time requires co-operation, structure, attention to detail and following a process throughout the project.