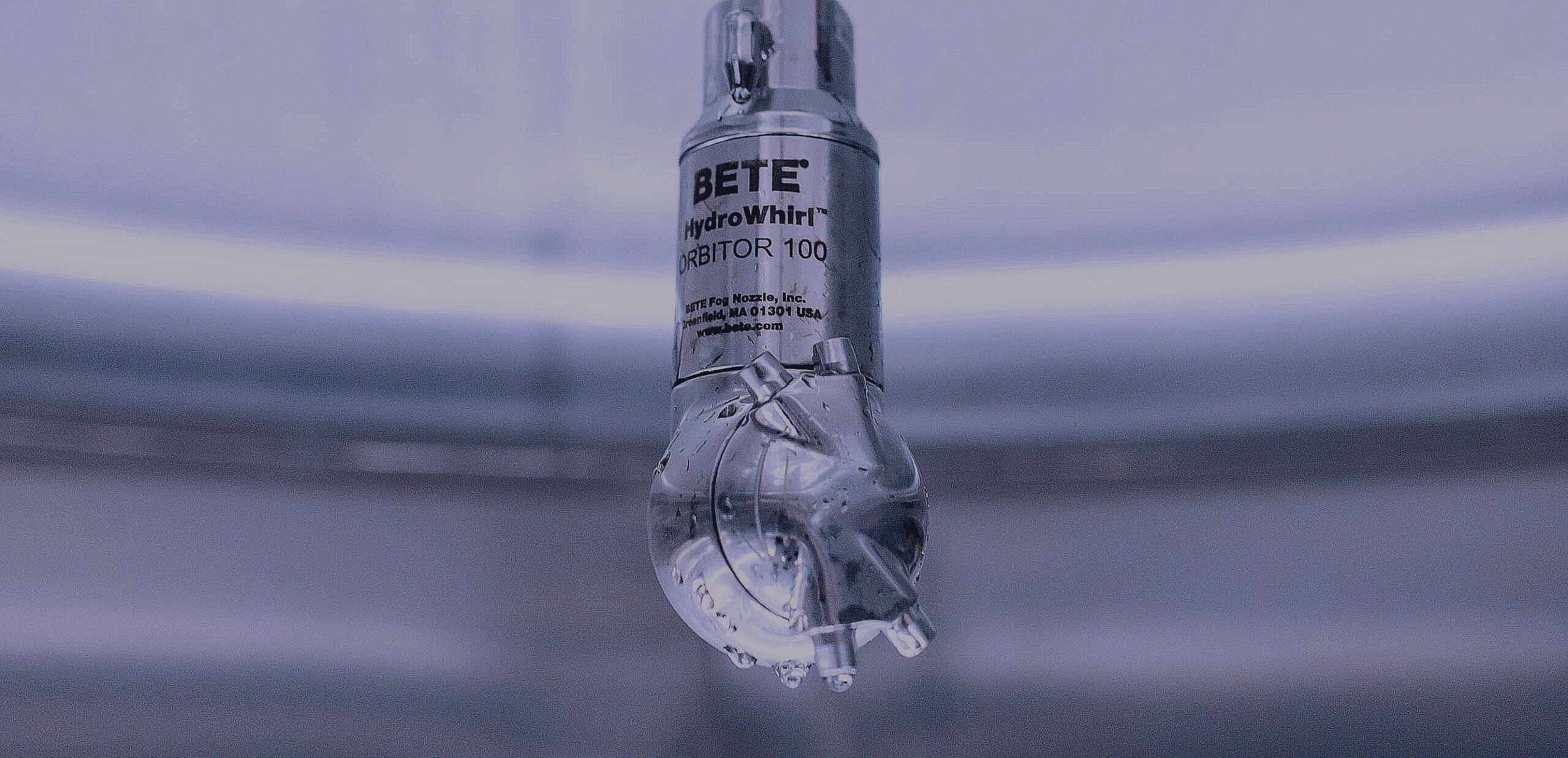
Liquid distributors
Liquid distributors ensure an even distribution of liquid over the entire cross-section of the packed bed.
A packed column requires a well-designed liquid distributor system in order to achieve an even distribution of liquid across the packed bed, thus optimising mass transfer across the entire operating range. Other important characteristics of liquid distributors include low gas-side pressure drop, low sensitivity to fouling and low overall height.
- Product information
- Technical data
- Documentation & videos
- Checklist process data
- General info Column internals
- Supplier information
- Send saved products to yourself, or as a quote request to Hansa
Ensure optimal liquid distribution in the column
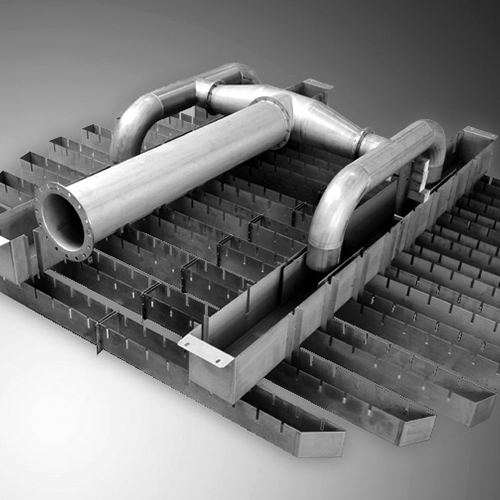
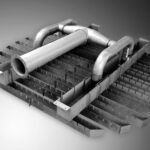
Factors taken into account when designing a liquid distributor for a specific process are:
- liquid load
- operating range
- liquid properties
- risk of fouling or foaming
- allowable liquid entrainment
The number of drip points generally ranges between 60-150/m², depending on the particular application.
To ensure an efficient process, the following criteria need to be met:
- even distribution of liquid
- low pressure drop in the gas phase
- low risk of clogging due to contaminants or solid particles in the fluid
- wide flow range
- minimise the amount of droplets entrained in the gas flow
- ensure even gas distribution
- prevent liquid-flow channelling in the bed or along the column wall
Different types of liquid distributors
Pan-type
Deck type
Trough type
Ladder type
Spray-nozzle type
Trough-type with integrated parting box
Listed below are RVT's different types of liquid distributors, liquid load, and recommended column diameter.
Model and Material | |||||||||||
---|---|---|---|---|---|---|---|---|---|---|---|
Design type | Liquid load m3/m2h | Recommended column Ø in mm | Metal | Plastic | Ceramic | ||||||
Pan-type | 0,3 - 200 | 100 - 1600 | M 150 T | P150 T | K 150 T | ||||||
Deck type | 5 - 200 | >200 | M 150 B | P 150 B | - | ||||||
Trough type | 0,3 - 50 | >600 | M 150 KK | P 150 KK | K 150 KK | ||||||
Ladder type | 4 - 100 | all sizes | M 150 RR | P150 RR | - | ||||||
Spray-nozzle type | 3 - 200 | all sizes | M 150 SR | P 150 SR | K 150 SR | ||||||
Trough-type with integrated parting box | - | - | M 150 KQ | P 150 KQ | - |
Other types or special designs on request.
Download PDF
Checklist important parameters
In order to offer an efficient and sustainable solution, we list here a number of parameters that are important to consider when selecting and sizing liquid distributors.
Sometimes it is difficult or even impossible to obtain information and data regarding the specific process. Together with our suppliers, we have extensive experience and we can make sound assumptions as a basis for designing the best solution for the process.
Operating data | |||||||||||
---|---|---|---|---|---|---|---|---|---|---|---|
Liquid | Unit | ||||||||||
Volume flow - min | m3/h | ||||||||||
Volume flow - mom | m3/h | ||||||||||
Volume flow - max | m3/h | ||||||||||
Liquid density | kg/m3 | ||||||||||
Dynamic viscosity of liquid | mPass | ||||||||||
Surface tension | mN/m |
Operating data | |||||||||||
---|---|---|---|---|---|---|---|---|---|---|---|
Gas | Unit | ||||||||||
Volume flow - max | kg/h | ||||||||||
Gas density (operating conditions) | kg/m3 |
Geometrical data | |||||||||||
---|---|---|---|---|---|---|---|---|---|---|---|
Data | Info/unit | ||||||||||
Column diameter | mm | ||||||||||
Opening for installation - Manhole | Yes/No | ||||||||||
Opening for installation - Vessel flange | Yes/No | ||||||||||
Packing - Random | Yes/No | ||||||||||
Packing - Structured | Yes/No | ||||||||||
Packing type | Please state if known | ||||||||||
Number of drip points | per m2 | ||||||||||
Material | Please state | ||||||||||
Optional material | Please state | ||||||||||
Preferred type of distributor | Please state |
Additional information | |||||||||||
---|---|---|---|---|---|---|---|---|---|---|---|
Data | Info/unit | ||||||||||
Fouling | Yes/No | ||||||||||
Foaming | Yes/No | ||||||||||
Type of feed pipe | Please specify | ||||||||||
Other requirements/additional information | Please specify |
Optimised performance in mass and heat transfer processes
For optimised performance in a mass or heat transfer process it is important to understand the underlying principles and parameters that are important to consider when designing a column for flue gas cleaning, flue gas condensation or stripping.
Founded in 1976, RVT Process Equipment is a leading supplier and manufacturer of droplet separators, packings, column internals and other products for mass and heat transfer processes.
RVT Process Equipment offers advanced engineering and technical support and has extensive experience in various processes and applications in the chemical and petrochemical industry, refineries, power plants, and pulp and paper. The R&D department houses fully equipped test units, available to carry out customer-specific tests when needed.
RVT Process Equipment has subsidiaries and manufacturing facilities in Knoxville, USA and in Kunchan, China.
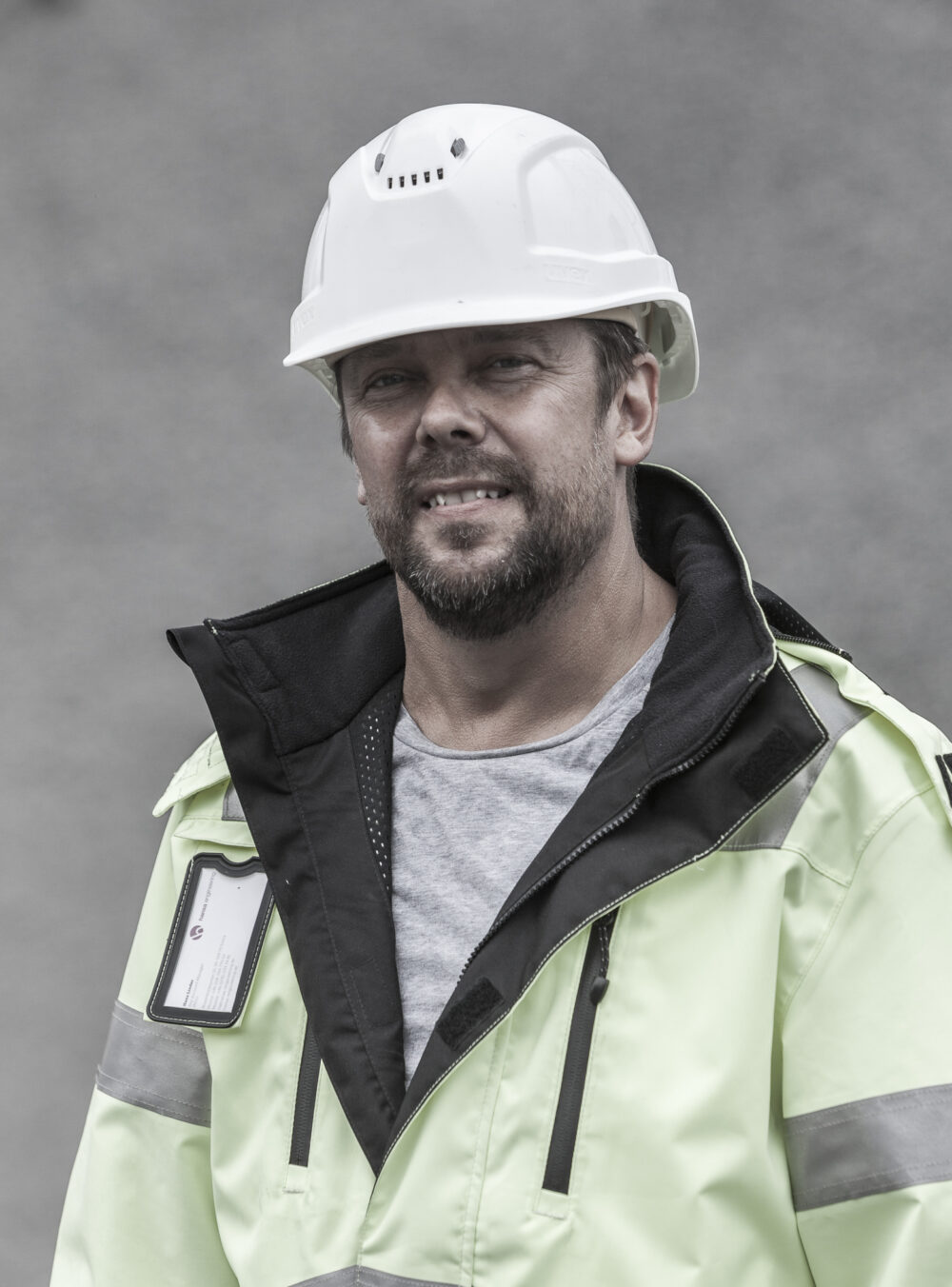
Our customer promise
Right solution, technical expertise and commitment is what you can expect from us as your partner or supplier.
Support & service
We offer the support you need to optimise your process, minimise risk and achieve a sustainable solution.
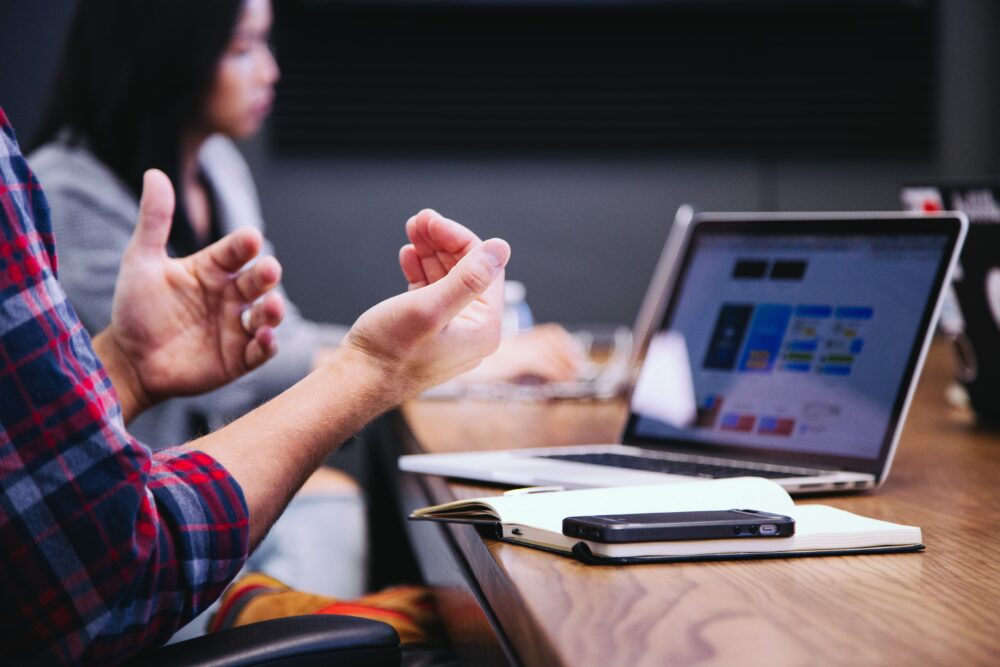
Right solution, delivered on time
Delivering the right solution on time requires co-operation, structure, attention to detail and following a process throughout the project.